Tipos de transmisores
Transmisor neumático: Se fundamentan en el principio que cumple el sistema tobera obturador que cociste en un tubo con un suministro constante de presión no superior a los 25 Psi que pasa por una restricción que reduce el diámetro al rededor de 0.1 mm y que en su otro extremo se torna en forma de tobera con un diámetro de 0.25 - 0.5 mm que esta expuesto a la atmósfera ocasionando un escape que es regulado por un obturador el cual cumple la misión de controlar el escape proporcional a la separación entre él y la tobera, la función de la tobera - obturador es que a medida que la lamina obturadora disminuya o aumente la distancia hacia la tobera ocasionara un efecto inversamente proporcional sobre la presión interna que es intermedia entre la presión atmosférica y la de suministro igual a la señal de salida del transmisor que para la tobera totalmente cerrada equivale a 15 Psi y totalmente abierta a 3 Psi.
Para la obtención de una salida eficiente y a causa de diminutos volúmenes de aire que se obtienen del sistema se le acopla una válvula piloto que amplifica, formando un amplificador de dos etapas.
La válvula servo-pilotada consiste en un obturador que permite el paso de dos caudales de aire los cuales nos determinan la salida mediante los diferenciales de presión entre las superficies uno y dos logrando vencer el resorte que busca sostener la válvula cerrada, aunque realmente existe una mínima abertura que lo que nos determina los 3 Psi como salida mínima. Las funciones de la válvula son:
Aumento del caudal suministrado o del caudal de escape para conseguir tiempos de respuesta inferiores al segundo. Amplificación de presión (ganancia),de cuatro a cinco para obtener la señal neumática de 3 - 15 Psi. Los transmisores neumáticos presentan las siguientes características:
-Un consumo de aire mas bajo para el caudal nulo de salida.
-Un caudal mayor de salida hacia el receptor.
-Una zona muerta de presiones de salida.
-Son de equilibrio de fuerzas.
-Son de acción directa.
Transmisor electrónico: Generalmente utilizan el equilibrio de fuerzas, el desequilibrio da lugar a una variación de posición relativa, excitando un transductor de desplazamiento tal como un detector de inductancia o un transformador diferencial. Un circuito oscilador asociado con cualquiera de estos detectores alimenta una unidad magnética y es así como se complementa un circuito de realimentación variando la corriente de salida en forma proporcional al intervalo de al variable en proceso. Su precisión es de 0.5 - 1 % en una salida estándar de 4 - 20 mA. Se caracterizan por el rango de entrada del sensor.
Transmisor inteligente: Son aquellos instrumentos capaces de realizar funciones adicionales a la de la transmisión de la señal del proceso gracias a un microprocesador incorporado. También existen dos modelos básicos de transmisores inteligentes:
El capacitivo que cociste en un condensador compuesto de un diafragma interno que separa las placas y que cuando se abren las placas es porque se realiza una presión este diafragma se llena de aceite lo cual hace variar la distancia entre placas en no mas de 0.1 mm. luego esta señal es amplificada por un oscilador y un demodulador que entregan una señal análoga para ser convertida a digital y así ser tomada por el microprocesador.
El semiconductor sus cualidades permiten que se incorpore un puente de whetstone al que el microprocesador linealiza las señales y entrega la salida de 4 - 20 mA.
Los transmisores inteligentes permiten leer valores, configurar el transmisor, cambiar su campo de medida y diagnosticar averías, calibración y cambio de margen de medida.
Algunos transmisores gozan de auto-calibración, auto-diagnóstico de elementos electrónicos; su precisión es de 0.075 %. Monitorea las temperaturas, estabilidad, campos de medida amplios, posee bajos costes de mantenimiento pero tiene desventajas como su lentitud, frente a variables rapidez puede presentar problemas y para el desempeño en las comunicaciones no presenta dispositivos universales, es decir, no intercambiable con otras marcas.
Ajustes
Como calibrar un transmisor:Chequeo y Ajustes Preliminares: Observar el estado físico del equipo, desgaste de piezas, limpieza y respuesta del equipo.
Determine los errores de indicación del equipo comparado con un patrón adecuado (según el rango y la precisión).
Llevar ajustes de cero, multiplicación, angularidad y otros adicionales a los margenes recomendados para el proceso o que permita su ajuste en ambas direcciones (no en extremos) excuadramientos preliminares. Lo cual reducirá al mínimo el error de angularidad.
Ajuste de cero: Colocar la ariable en un valor bajo de cero a 10 % del rango o en la primera división representativa a excepción de los equipos que tienen supresión de cero o cero vivo, para ello se debe simular la variable con un mecanismo adecuado, según rango y precisión lo mismo que un patrón adecuado.
Si el instrumento que se esta calibrando no indica el valor fijado anteriormente, se debe ajustar del mecanismo de cero( un puntero, un resorte, reóstato, tornillo micrométrico, etc).
Si el equipo tiene ajustes adicionales con cero variable, con elevaciones o supresiones se debe hacer después del punto anterior de ajuste de cero.
Ajuste de multiplicación: Colocar la variable en un valor alto del 70 al 100 %.
Si el instrumento no indica el valor fijado, se debe ajustar el mecanismo de multiplicación o span ( un brazo, palanca, reóstato o ganancia).
Repetir los dos últimos pasos hasta obtener la calibración correcta para los valores alto y bajo.
Ajuste de angularidad:
Colocar la variable al 50% del span.
Si el incremento no indica el valor del 50% ajustar el mecanismo de angularidad según el equipo. Repetir los dos últimos pasos 4 y 5 hasta obtener la calibración correcta, en los tres puntos.
Nota: Después de terminar el procedimiento se debe levantar un acta de calibración, aproximadamente en cuatro puntos: Valores teóricos contra valores reales ( lo mas exactamente posible), tanto ascendente como descendente para determinar si tiene histéresis.
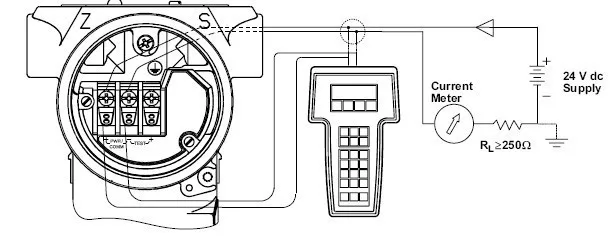